The Analysis Of China's Automotive Die Casting Industry
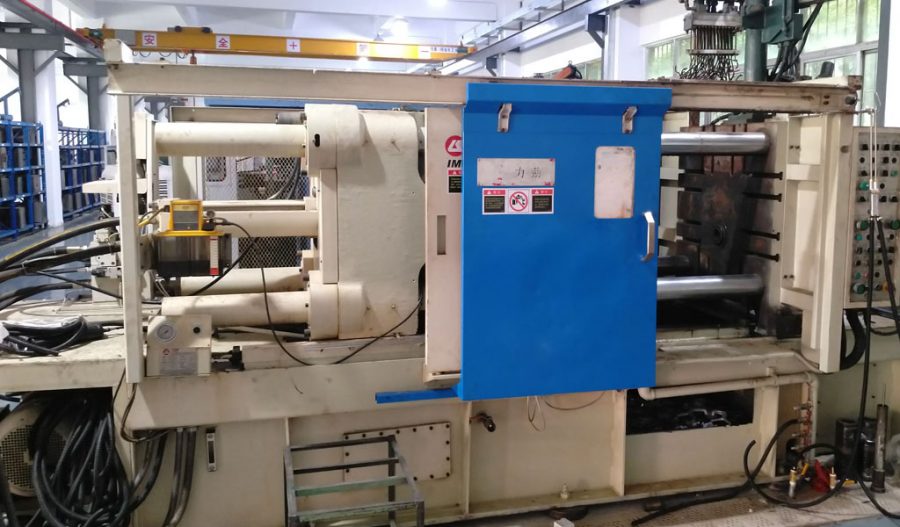
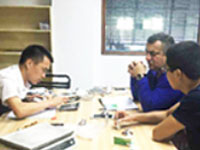
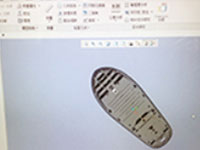
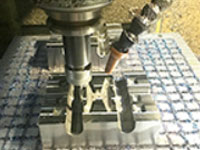
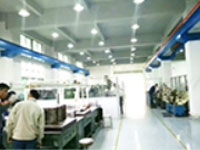
The metal materials used in die casting are mainly aluminum alloys, magnesium alloys, zinc alloys and copper alloys. Since aluminum alloy die castings are widely used in the automotive industry, they account for a high proportion of die castings. According to the statistics of China Foundry Association, the proportion of aluminum alloy die castings in die castings is about 85%.
Market overview of die casting industry
(1) Overview of the international market
In recent years, with the development of the global economy, the demand for precision die castings in many fields such as automobiles, 3C products, communication infrastructure equipment, household appliances, and medical equipment has steadily increased.
At present, the market maturity of die casting parts in developed countries is relatively high. With the improvement of die casting equipment and process technology, more and more ferrous metal castings are replaced by non-ferrous metal die castings such as aluminum alloy and magnesium alloy. The production and consumption of global die castings are mainly concentrated in the United States, China, Italy, Germany, Mexico, Japan and other countries.
For developed countries, due to their leading advantages in equipment and technology, china automotive die-casting industry is generally dominated by high-quality and high-value-added die-casting such as automobiles, communications, and aviation.
The number of die-casting enterprises in developed countries is small, but a single enterprise has a large scale and a high degree of specialization, and has strong advantages in capital, technology, and customer resources.
According to the "State of the Industry Report and Research & Development" released by NADCA in October 2013, in 2012, my country was the world's largest producer of die castings, accounting for 34% of the world's total output.
(2) Overview of the domestic market
With the gradual accumulation of downstream manufacturing industries in China, my country's die-casting industry has also developed by leaps and bounds with the improvement of China's overall industrialization level, and has gradually developed into the world's largest die-casting country. From the perspective of the output of die-casting parts, with the continuous and rapid development of my country's automobile, communication infrastructure, 3C products, equipment manufacturing, home appliances, electromechanical instruments, light industry and other industries, as well as the transfer of foreign die-casting industries to China, die casting china industry has entered a new normal of steady growth.
As more and more high-end manufacturing industries transfer their production capacity to China, China's die-casting industry is also continuing to upgrade its structure in the process of growth, and the proportion of precision die-casting parts is gradually increasing. As of the end of 2013, the proportion of China's die-casting products used in the automotive industry has exceeded 70%, which is basically the same as that of developed countries.
As the most important category of products in the die-casting industry, the demand for auto parts, especially aluminum alloy die-casting parts for automobiles, will largely affect the overall development prospects of the die-casting industry. From the perspective of the structure of the whole car, in addition to the large number of precision die-casting parts used in the automobile engine, gearbox, transmission system, steering system, and electronic control system, aluminum alloy die-casting parts have also been used for large components such as the body frame.
Market overview of automotive die casting industry
As the most important application field of die-casting products, a large number of precision die casting parts are used in automobile engines, gearboxes, transmission systems, steering systems, and electronic control systems. The demand for auto parts will greatly affect the overall development of the die-casting industry. prospect.
As people pay more and more attention to automobile energy saving and environmental protection, the automobile industry has shown a trend of replacing steel and iron with aluminum in the past three decades, and this trend is still continuing. At present, the global aluminum alloy die casting market for automobiles is showing a rapid development trend as a whole.
In addition, in addition to aluminum alloy die castings, zinc alloy, magnesium alloy and copper alloy die castings are also used in automobiles.
The demand for aluminum, zinc and other metal die castings in the automotive industry will continue to grow in the future, which is mainly affected by the following factors:
China's auto industry will maintain a relatively fast development speed
Since the reform and opening up, with the rapid growth of my country's economy, the automobile die casting industry has also achieved rapid development. In 1980, my country's automobile production was 222,300 units, and by 2016, it increased to 28,120,000 units, an increase of 125.49 times. In recent years, affected by the international and domestic economic situation, the growth rate of my country's automobile production has declined, but due to the high base, the annual new automobile production is still quite large.
In 2016, my country's private car ownership was 146 million, with 36 cars per 100 households, far below the level of developed countries. Therefore, china auto industry still has a lot of room for development in the future.
The trend of lightweight automobiles
The so-called lightweight of the car is to reduce the curb weight of the car as much as possible on the premise of ensuring the strength and safety performance of the car, thereby improving the power of the car, reducing fuel consumption and reducing exhaust pollution. For the lightweight of the whole vehicle, different components can contribute to different degrees. The lightweight of the body, interior and exterior trim, and power system is of great significance for reducing energy consumption during vehicle driving. Aluminum alloy materials are lightweight, recyclable and easy to form. Theoretically, an aluminum car can reduce the weight by 30%-40% compared with a steel car, among which the aluminum engine can reduce the weight by 30%, the aluminum radiator is 20%-40% lighter than the copper one, and the all-aluminum body is 40% lighter than the steel one. % or more, the weight of automobile aluminum wheels can be reduced by 30%. Therefore, aluminum alloy material is one of the most ideal materials for automobile lightweight.
Since 2011, due to the consideration of reducing greenhouse gas emissions and reducing the dependence on fossil energy, the indicators of automobile fuel consumption have been continuously improved. As one of the key technologies for vehicle energy saving, light weight has a significant energy saving effect. A 10% weight reduction for gasoline passenger vehicles can reduce fuel consumption by 3.3%, and a 15% weight reduction can reduce fuel consumption by 5%; for diesel passenger vehicles, fuel consumption can be reduced by 3.9% and 5.9% respectively.
Lightweight also has a good energy saving effect on electric vehicles (including plug-in hybrids). Weight reduction of 10% and 15% can achieve 6.3% and 9.5% of power consumption, respectively. The researchers also conducted related experiments on trucks of different energy categories, and also showed good energy-saving effects.
Reducing the weight of the car can reduce the engine load, improve the driving performance of the car, effectively reduce the braking distance, and make the steering and cornering process more flexible, thus making the car more stable, and the aluminum alloy structure can absorb and disperse more energy when it is impacted. , thus more comfortable and safe. Affected by this, the penetration rate of aluminum used in various major components of automobiles will increase significantly in the next decade. According to Ducker Worldwide, the penetration rate of aluminum hoods will increase from 48% in 2015 to 85% in 2025, and the penetration rate of aluminum doors will increase from 6% in 2015 to 46% in 2025. Specifically reflected in the average aluminum consumption per bicycle, the average aluminum consumption per vehicle in North America was 54kg in 1980, and increased to 154kg in 2010. It is expected that the average aluminum consumption per vehicle will reach nearly 325kg by 2025.
(3) The development of new energy vehicles will further promote the demand for metal die castings
One of the main problems of current new energy vehicles is the short cruising range, and lightweight design has become the main measure for reducing weight and consumption of new energy vehicles. Taking Tesla (TESLA) Model S as an example, its total weight is 2,108kg, and the weight of the battery alone exceeds 500kg. In addition, the drive motor increases the weight of the whole vehicle; while the total weight of the engine of a traditional car is generally 80-160kg. The mileage of a 70L gasoline car can reach 700-900Km, while the cruising range of an electric vehicle with a 500kg battery is only about 400Km. Therefore, increasing the proportion of automotive aluminum alloy die castings is the main measure to reduce the weight of new energy vehicles.
With the release and implementation of my country's automobile energy saving and emission reduction policies, my country's new energy vehicles have shown a rapid development trend in recent years. In 2016, the cumulative production of new energy vehicles was 517,000, an increase of 49.99% over 2015. Among them, the output of pure electric passenger vehicles increased most significantly, up 73.10% compared with 2015; the production of pure electric commercial vehicles increased by 50.20% compared with 2015; the output of plug-in hybrid electric passenger vehicles increased by 29.9% compared with 2015. From January to June 2017, the cumulative production of new energy vehicles was 212,000, an increase of 19.77% over the same period of the previous year. Among them, the output of pure electric passenger vehicles increased most significantly, up 30.60% over the same period of the previous year.
New energy vehicles have stricter requirements on body weight than traditional energy vehicles, so more lightweight aluminum alloy die-casting parts are used. For example, 95% of the Tesla (TESLA) Model S series models use aluminum alloy materials. The sustained and rapid growth of new energy vehicles will form a strong impetus for the development of the automotive aluminum alloy die casting industry.
Post a Comment
Note: Only a member of this blog may post a comment.