Which Metal Should You Choose For Die Casting?
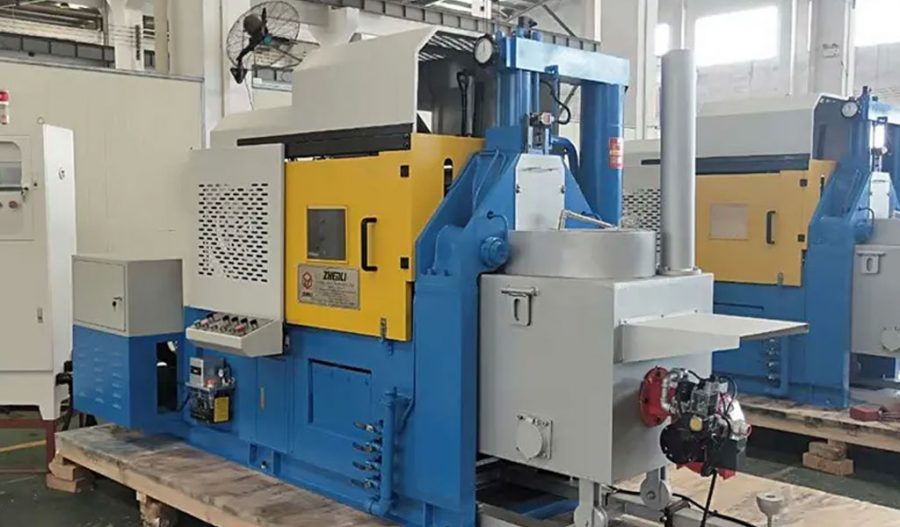
If you're designing volume die casting of a part or product, choose a manufacturing process that can build it using the same material. In metal die casting, you can consider the process of cold chamber die casting process, which can build parts from different metal materials one layer at a time. Cold chamber die casting services is a injection chamber and the injection punch are not immersed in the molten metal, but a quantitative amount of molten metal is poured into the injection chamber and then injected. ,. This way, it can create highly complex shapes when other manufacturing methods can't.
However, you need to know the best metals that can be used for your display die casting or other project. Choosing the correct metal will ensure optimum results and an effective die casting process that will improve your chances of success.
Which metals can be used in die casting?
Which Metal Should You Choose For Die Casting?Reputable manufacturers offer a range of materials, such as aluminum, zinc, copper, and magneium. These metals come with various properties, making them ideal for a range of applications. For instance, if you require volume production of automotive parts, pipes, or valves; aluminum and aluminum alloy can be a good option for offering outstanding corrosion resistance.
Metals to avoid in die casting
Any metal may be used in die casting if it can be supplied as an appropriate metal. However, materials that burn instead of melt at high temperatures should be avoided as they cannot be melted safely or sintered. Metals to avoid in die casting:
- Stainless Steel
- Titanium
- Greek Ascoloy.
- Carp 49
- Hastelloy
- Nitronic-60
- Inconel
- Hymu 80
- More
Benefits of Die Casting with High Volume
High Volume Thin Wall Die Casting and cnc machining is a versatile metal manufacturing technology that lets you build functional metal rapid prototypes and parts with complex shapes or geometries. It's used extensively in the medical, automotive, and aerospace industries for fulfilling part consolidation and weight-saving application requirements. Creating prototypes and low-volume end-use parts out of Thin Wall Die Casting metals are typically detailed but not necessarily structurally sound.
Post a Comment
Note: Only a member of this blog may post a comment.